Contact Person: M. Vlachou [marvlach@gmail.com]
The present project is dealing with flow boiling in a single rectangular channel. The main objectives of the current work are (a) to understand the phenomena that govern flow boiling in a small channel with a hydraulic diameter of a few millimeters and (b) to determine the experimental conditions that will allow currying away high heat fluxes. For this reason the effect of the following parameters on flow boiling heat transfer characteristics are investigated:
- channel’s geometrical characteristics (height)
- channel’s orientation (0-360º)
- heat flux
- mass flow rate
- topography of the heated surface (plain& treated)
Experiments are conducted with subcooled water (Twater, inlet <Tsaturation) and take place in both terrestrial (AUTH) and hypergravity conditions (Large Diameter Centrifuge at ESA/ESTEC). The experimental setup used to for the experiments at AUTh is shown in figure 1, while the experimental setup placed inside the gondola of the LDC is shown in figure 2.
The parameters that are monitored during the experiments are:
- Working fluid flow rate
- Working fluid temperature (inlet: one position and outlet: two positions)
- Heated surface temperature (six positions)
- Pressure in the test section (inlet and outlet)
- High speed video recordings (side and top of the channel at 8000 & 1000 fps respectively)
- Infrared images (test section)
- Void fraction of the two phase exit flow by a novel technique, IVED (In-Vivo Embolic Detector, ESA Project).
Surface modification techniques (i.e. laser engraving, figure 3) are applied in order to increase flow boiling heat transfer coefficient.
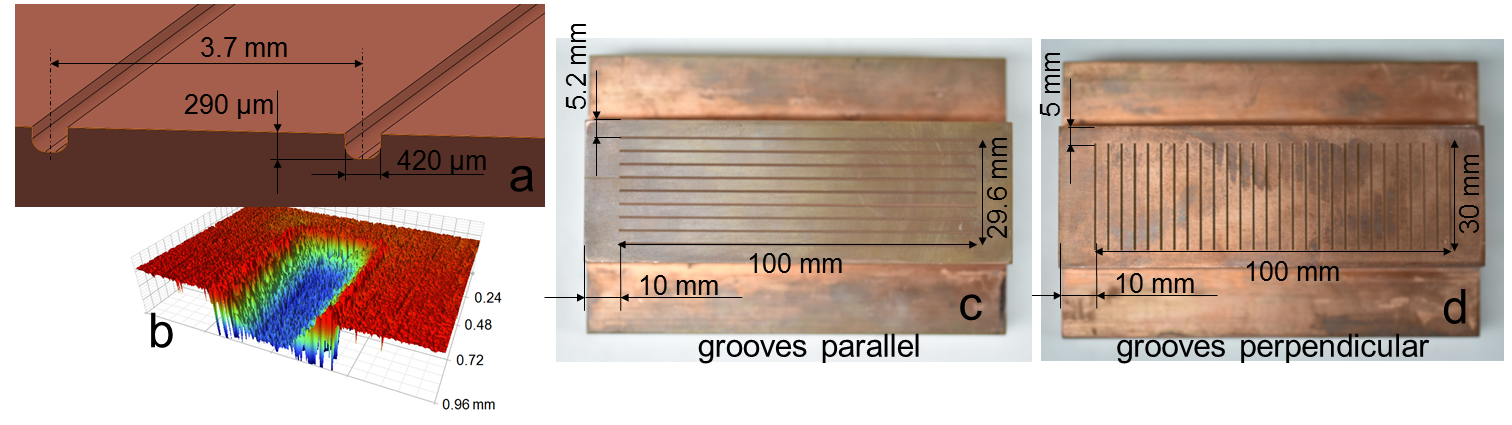
Figure 3: Images of grooved surfaces (a) schematic graph, (b) 3D image from profilometer, (c) surface with grooves parallel to the flow and (d) surface with grooves perpendicular to the flow.
Summary
Working conditions such as mass and heat flux, channel size, channel inclination, heated surface topography and hypergravity affect heat transfer performance, as expected. Assessing temperature and bubble dynamics provides evidence to explain the behavior of the heat transfer mechanisms during those changes (Figure 4-5, Video).
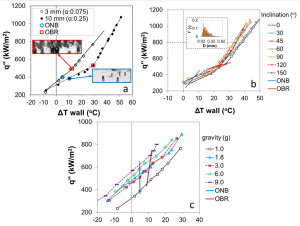
Figure 4: Effect of (a) channel height (at inclination= 0o) and (b) channel inclination (at height=10 mm) (c) gravitational acceleration (at height= 3 mm and inclination= 0o) on boiling curves at Earth-gravity (same mass flux rate, 330 kg/m2s). ONB: Onset of Nucleate Boiling, OBR: Onset of Bubbly Regime

Figure 5: Effect of surface topography (a) on boiling curves (i) channel height= 10 mm and (ii) channel height= 3 mm and (b) on bubble interaction inside a groove when grooves are parallel to the flow (at mass flux rate= 330 kg/m2s and inclination=, 0o).
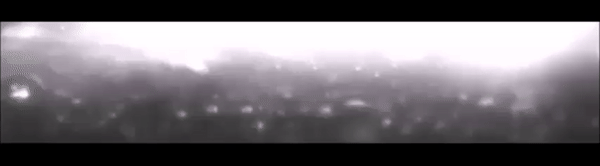
Video: Side view, 8000 fps, real duration 32 ms, window size 1.1×5.4mm (at 3 g, mass flux rate= 330 kg/m2s, heat flux= 690 kW/m2, height= 3 mm, inclination= 90o)
Flow boiling over modified surfaces in mini channels – extension
As an extension of the above study, new structured boiling surfaces are designed and tested using an experimental flow boiling setup (Figure 6) using subcooled water as the working fluid. This experimental setup consists of a mini-channel (w 40 x h 3mm) and permits the experimental determination of the working conditions that maximize heat removal and also offers simultaneous monitoring of the following: working fluid flow rate, working fluid temperature, heated surface temperature & high-speed video recordings (top view of the boiling channel at the entrance and the exit of the channel at 4000fps). Images of the five new structured surfaces are shown in Figure 7.

Figure 7: Images of the five different structured surfaces (a) chessboard, (b) oblique fins, (c) zig zag, (d) lego and (e) piranhas
Video: Top view at the exit of the boiling channel using the zig zag surface, 4000 fps, mass flux rate= 200 kg/m2s, heat flux=1000 kW/m2, channel height= 3 mm, inclination= 90o)